This seems to be one of those hot topics where everyone has an opinion and a lot of people seem quick to criticise other people’s methods.
When I first started sharpening chisels and plane blades it would take me hours and hours… and to be honest it still does take me a long time when restoring an old chisel or flattening the back of a new cheaper chisel like the ones I received for xmas (Aldi chisels – rubber handle version not wood handled ones Paul Sellers writes about).,, but for maintaining a sharp edge the process is now quick, easy and enjoyable.
When its all said and done, I used to put far too much thought and worry into how to sharpen my tools. From my current perspective I now see sharpening as being far simpler then the volume of videos and blogs and forum posts would suggest… so I figured I would add yet another blog post on the subject! Hey I never claimed to be S-M-R-T !
I believe the topic of sharpening gets so much air time because most of us hobbyists don’t really know a few things; how sharp is sharp enough? or are we really doing things the ‘right’ way? Typically we have no formal training and the hours in the shop are few and far between.. as a result of all these things some of us are almost paralysed by the prospect of doing something incorrectly… The good old Analysis Paralysis.
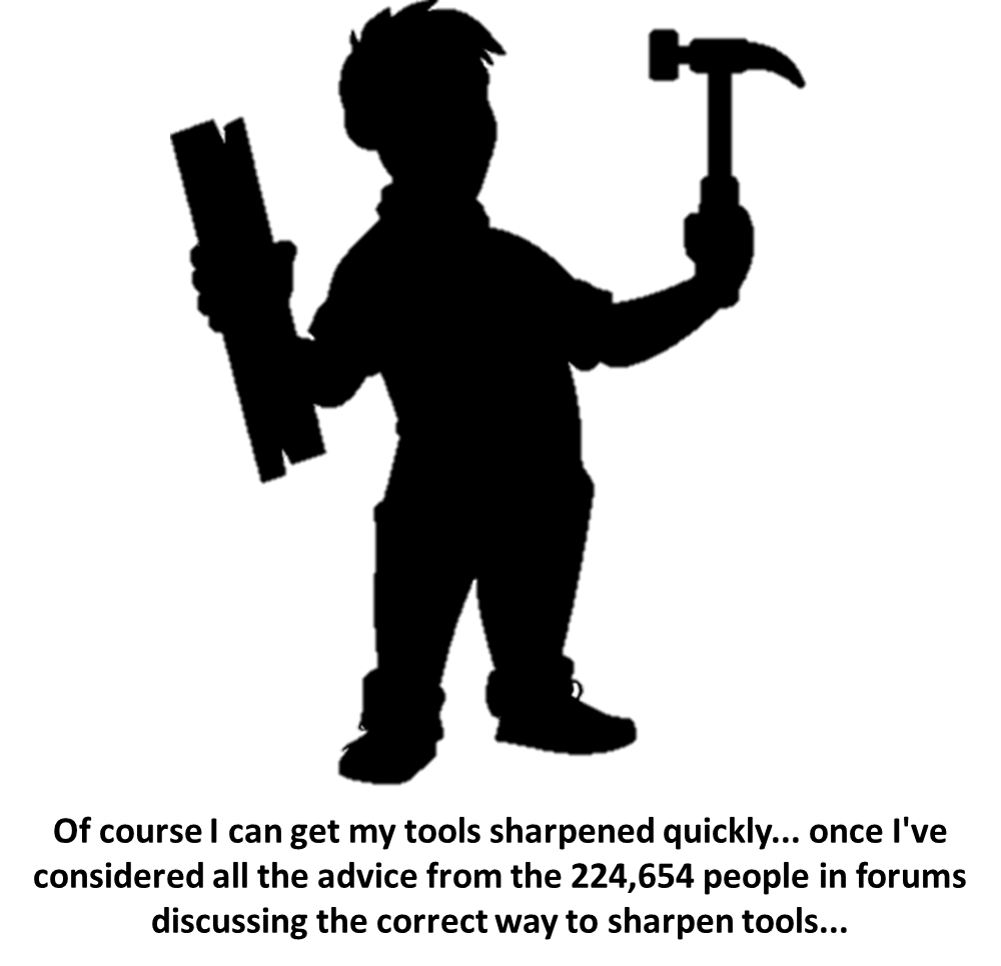
When it is all said and done.. regardless of the sharpening medium you choose to use… all you are aiming for is two flat surfaces that intersect to make a sharp edge… simple right?!
It does NOT matter what abrasive medium you choose to use to achieve this.
Some possible options include sandpaper on granite or glass, diamond stones, water stones or …. something else…
The steps you need to take to create that nice intersection between two surfaces is broadly;
- Flatten the back of tool and polish it
- Flatten the angled surface of the tool that interests with the flattened ‘back’ of the tool
- This is the primary bevel
- Polish/hone the surface that intersects with the ‘back’ of the tool.
- This can be the polishing/honing of primary bevel or,
- This can be the polishing/honing of a secondary bevel
Flattening the back of the tool
I happen to have a spare optical breadboard at home that is reasonably flat, so I use this as the surface that I put some wet and dry sandpaper onto when I’m flattening the back of a chisel or a plane blade for the first time.
You could use granite or thick float glass or some other flat stable surface if you are also going to try the sandpaper approach.
For the old chisels I’ve restored, and the new Aldi chisels, I start off at #120 grit, then #240, then #400. After #400 I generally move over to my Shapton stones – partly because I have the Shapton stones and partly because I don’t typically have higher grits of sandpaper in the shed – I have tried using up to #3000 grit sandpaper and achieved good results, but normally I head to the Shapton stones after #400 grit wet dry sandpaper.
Each time I go up a grit in sandpaper, or on the Shapton stones, I try and move the chisel/blade in a perpendicular direction to how I moved it on the previous grit. This way it makes it easier to see when I have fully removed the scratch marks from the previous grit and am then ready to move to the next grit.
Sometimes I find it easier to not change the direction that I move the chisel/blade as I change grits… and I don’t loose any sleep over not changing directions. You can still see when you have removed the previous scratch marks… so just do what feels good to you at the time and whatever works for you.
Then I move to the Shapton KUROMAKU stones. These stones are colour coded with each colour representing a different grade of coarseness. I start on the orange (1000) stone, then move to the violet/’wine’ (5000) before finishing up on the green/’melon’ (8000) stone.
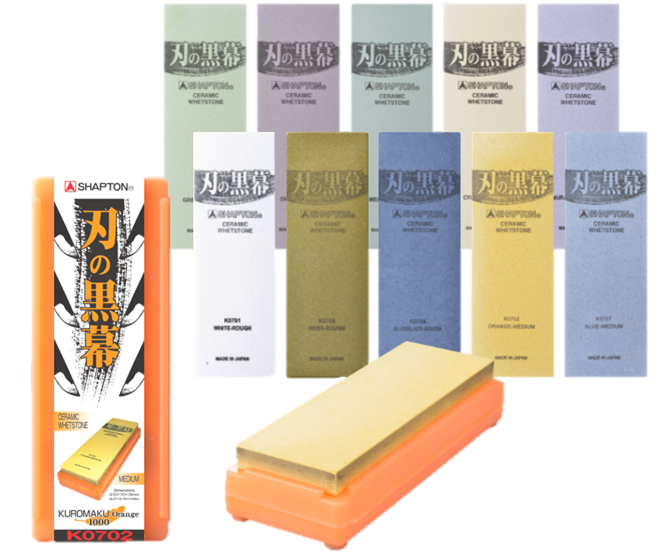
As I am trying to flatten the backs of the chisels/blades it is obviously important to make sure the stones are flat. I use a Tsuboman ATM75-4E Atoma #400 diamond plate to flatten my stones. I’m not sure if it is the best approach, but it has been working great for me so far.
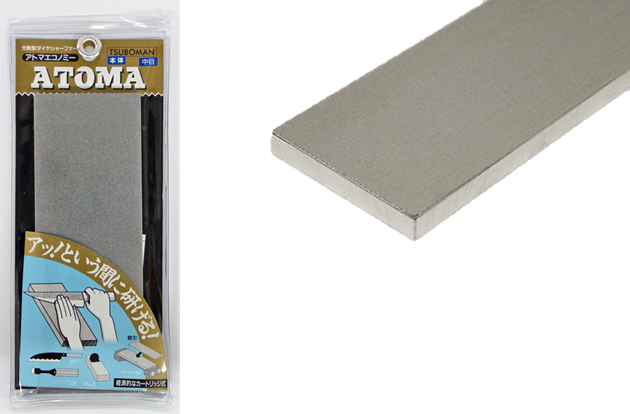
For chisels you probably only need to flatten the 20 mm or so closest to the cutting edge, however I tend to find myself flattening sometimes up to 100 mm. I figure you typically only need to spend time flattening the back of the chisel once, so why not spend a little bit more time flattening a larger area… mainly because I think it looks good! in reality you are only really going to need 10-30 mm for registering off existing surfaces when using the chisel.
For plane blades you only need the last few mm to be flattened/prepared.. but again I find myself flattening a larger section, 50-60 mm or so, because I enjoy the process and think it looks good. If pressed for time or in a rush, then obviously you don’t need to flatten and polish as large of an area on the back of your chisels and plane blades.
For plane blades it would also be reading about the ‘rule’ trick promoted by Lie-Nielsen Toolworks and David Charlesworth (amongst others) where you put a metal rule on the edge of the stone so that you only polish the very tip of the back of the blade. Check out the Lie-Nielsen website for more details including a nice pdf that is a great guide to their sharpening method. https://www.lie-nielsen.com/nodes/4114/sharpening
Create the Primary Bevel
There are so many ways to achieve this. Grinders, sandpaper, diamond stones, water stones etc. It doesn’t matter which method you pick, they will all work.
I’ve tried freehand sharpening and had better success then I was expecting given all the discussions about muscle memory and rounding over of the cutting edge etc… but ultimately I have ended up back using a jig.
The jig is slightly slower, but it gives me consistent results and I personally like the feeling of holding the jig in my hands when I sharpen.
I did also like the feeling of accomplishment when I successfully hand sharpened something… so to me it seems like a personal choice about what brings you enjoyment while carrying out the task.
I enjoy the process with using the jig; getting the jig out, inspecting it for any contamination I missed cleaning off it last time I used it, setting the guide onto the jig to give me the angle I want on the chisel/blade, the feel of the jig in my hands and I move it back and forth over the abrasive medium (while listening to some music).
After reading Michael Pekovich’s book, The Why & How of Woodworking: A Simple Approach to Making Meaningful Work, I’ve been more aware of the tasks that I used to rush in an attempt to get back to the woodwork and I’m now enjoying the process of tasks like sharpening, cleaning, serving the machines etc rather than seeing them as obstacles of me getting a project done.
SO… people will have different reasons to pick the approaches they do… but basically all the approaches will work, so try a method, a medium and master it before trying something else. The different methods and abrasive mediums all work – you just need to practice one approach until you are getting good results.
Honing the angled surface
Some people do this to the primary bevel, some people add a micro-bevel to speed things up as you don’t need to remove as much metal to get a good sharp intersection between the back of the tool and the angled surface you are polishing/honing.
I am lucky enough to have a Veritas MK II honing guide. I have both the narrow blade head and the camber roller… so I have the camber roller permanently attached to the standard honing guide for my plane blades and the narrow-blade head attached to the standard roller that came with my MK II honing guide.

Using the MK II guide I simply rotate the micro-bevel knob to the micro-bevel position before using my 5000 and 8000 Shapton stones to produce a nice polished surface that makes a nice sharp edge when it intersects with the back of my chisel/blade.

I used to then move onto a strop and some honing compound, but I found the leather I was using for the strop was too soft and it would actually round over the cutting edge and make it duller then it was prior to stropping.
I tried stropping using some MDF and the honing compound, and this worked better then my kangaroo leather strop… however I personally didn’t notice too much difference to using the 8000 Shapton stone but making sure not to apply hardly any downward pressure on the blade.
As with any abrasive you use, let the abrasive do the work and do not push the chisel/blade down into the abrasive.
And that is basically it as far as how I carry out the sharpening of my chisels and plane blades. Some people might like to go to finer stones then I use.. and if I end up with a finer stone in my shed I’m sure I’ll use it, but for now going up to the 8000 Shapton stone (remembering to put minimum downwards pressure on the chisel/blade) seems to produce tools that are sharp enough for me at the moment.